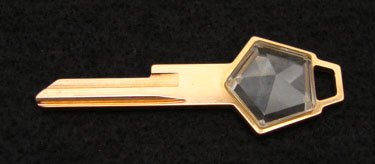
In the grand old days before we, and probably our fathers, were born, Chrysler locks were built by Yale and Ford locks were built by Hurd. These were the common design called “pin tumbler” locks; they were pretty much identical to the locks on houses.
These locks work best with gravity helping the tumbler springs to seat the pins, and the same gravity keeps dust and water out of the pin holes; so the design uses the key in the “tooth up” orientation.
Chrysler keys went in the normal way
GM locks were built by Briggs & Stratton (the same people that build lawnmower engines), using a design called “flat tumbler side locking bar.” This is a more secure locking system, virtually pick-proof, but does have some other limitations. Key and component wear is decreased with the key in the “tooth down” orientation.
There is another type of lock called “wafer tumbler,” but in American cars up to the late 1980s, these were pretty much only used on glove boxes. These locks work well in about any position, but the design isn’t as secure — or at least it wasn’t, until double sided keys became the norm. Making the tumblers work on both sides of the key, and having twice as many tumblers, made them harder to manipulate without the key.
The modern design of these locks was pioneered by the foreign automakers in the 1970s, and some high end cars have furthered that technology with designs that work on four sides of the key and have over 20 tumblers, in some cases combining it with a sidebar like the old GM locks. Security was enhanced with electronic chips, a technology pioneered by GM in the 1980s.
I left the locksmith trade in the mid-1990s, partly because locks were getting what I termed “locksmith proof” by then. A simple lock failure that, at one point, could have been fixed in an hour two from the old service truck, was being transformed into a situation requiring the car to be towed to the shop with a day or two of time to fix, some of which was waiting for the manufacturer to ship parts not available at the dealership. When I visited my brother, who is still a locksmith, I was amazed that some of the cutting edge technology that I had to deal with then is now as obsolete as the mini pin tumbler Hurd locks on Fords from the 1950s was when I was a locksmith.
By the way, one of the common house calls when I was a locksmith was repairing house locks for people who had installed their own — GM car owners who had installed the house locks in the tooth down orientation, resulting in frozen tumblers and a key that wouldn’t work.
Richard, d’you remember (I’m betting you do) the Briggs & Stratton ignition locks used in Saginaw steering columns on GM cars, that eventually wore such that the key could be removed in any position, not just “Lock”? That apparently caused a great deal of trouble and an even bigger amount of mythological misunderstanding for at least one man in Canada. I was amused to encounter the same “failure”—in quotes because I regarded it as a nice convenience—in the Acustar column years later on a ’91 Dodge (not this one, which was in another ’91 Dodge).
The idea of pins on the bottom is nothing but trouble. In actuality, they only collect moisture and dirt because there is no way for it to drain. Besides, the dirt and moisture must travel all the way down to the bottom of the pins and cylinders. Pins on top do not allow the moisture and dirt to accumulate in the first place, because gravity keeps it away. I also have a hard time believing that there is that much difference that gravity will make in a properly lubed lock. The pins will still retract and fall back into place anyway.
Right now my Chevy pickup has a frozen pin section on the door in the shade, when it worked well in warmer weather. It was also parked after it had been driven and had everything warmed up. Of course I will have to add deicer now.